In high-risk industries like construction, mining, forestry, and agriculture, heavy equipment plays a vital role in daily operations. However, along with these powerful machines comes the potential for serious accidents, including “near miss events” This article explores what a near miss is, the causes of near miss incidents, their impact on safety and morale, and best practices to create a safer work environment on heavy equipment job sites.
Table of Contents
Introduction to Near Miss Events in Heavy Equipment Operations.
In heavy equipment operations across construction, mining, forestry, and agriculture, safety is paramount. Near miss events (like workers nearly being struck by machinery or vehicles narrowly avoiding collisions due to miscommunication) highlight potential hazards, indicating that safety protocols, equipment operation, or site management need improvement even when no harm occurs.
Defining a “Near Miss”
The term “near miss” refers to an unplanned event that had the potential to cause injury, damage, or loss but, fortunately, did not. In other words, a “near miss” is an incident where an accident was narrowly avoided but had all the ingredients for potential harm or damage. For example, a worker standing in a blind spot while an excavator is operating nearby may result in a near miss if the operator notices in time to stop. While everyone escapes unharmed, this incident exposes risks that could lead to severe accidents if left unaddressed.

The Importance of Near Miss Reporting.
- Near miss reporting captures valuable data on situations that could have led to serious consequences, revealing underlying risks. Analyzing these incidents allows safety teams to identify patterns and implement targeted safety measures to eliminate hazards before they cause harm.
- A strong near miss reporting system reinforces a culture of safety and accountability. When employees feel empowered to report incidents without fear, they become more vigilant and invested in safety, helping prevent accidents and creating a safer work environment for everyone.
- Near miss reporting turns close calls into learning opportunities, enabling teams to better manage risks and maintain safety, thus protecting workers and enhancing industry efficiency and safety standards.
Common Causes of Near Misses with Heavy Equipment.
The Bird’s Safety Triangle, also known as the accident triangle, reveals that for every fatal or serious injury, there are approximately 29 accidents with minor injuries and 300 minor accidents (near miss events) with no injuries. This statistic underscores a critical opportunity for proactive intervention to prevent incidents from escalating into severe outcomes.

Analyzing common factors behind near misses with heavy equipment across industries such as construction, mining, forestry, and agriculture enables operators, supervisors, and safety managers to implement targeted measures, reducing serious incidents by addressing unmitigated risks. Common factors include:
- Operator Error: Human error is a frequent cause of near miss events with heavy machinery. Fatigue, distraction, or insufficient training can lead to misjudgments, overlooked hazards, and unsafe speeds, creating serious close calls.
- Equipment Malfunction: In high-intensity industries, machinery wear requires consistent and proactive maintenance. Equipment malfunctions, such as brake failures or hydraulic system issues, often lead to near miss events, emphasizing the need for predictive solutions.
- Environmental Hazards: Unpredictable conditions (like uneven terrain, poor visibility, and extreme weather) often lead to near miss events in construction, mining, or forestry. Operator training and safety protocols are essential for adapting to these challenging environments.
- Poor Communication: Effective communication is crucial in team-based heavy equipment tasks, where breakdowns between operators and team members can lead to near misses. Using hand signals, radios, and spotters helps prevent misunderstandings, ensuring safer operations on site.

rations.
7 Practices for Preventing Near Misses in Heavy Equipment Operations.
Preventing near miss events in heavy equipment operations is essential for safety in high-risk industries. Though near misses cause no immediate harm, they reveal potential hazards. Implementing best safety practices helps companies reduce near misses and protect workers effectively. Key strategies include:
- Regular Equipment Inspections: Routine inspections and strict preventative maintenance are essential for heavy equipment to ensure safe, reliable operation. Regular checks prevent malfunctions and hazards, reducing the risk of near misses and accidents.
- Proper Training for Operators: Well-trained operators are essential for safe machinery use, requiring comprehensive, equipment-specific training covering features, controls, limitations, and emergency protocols. Regular refresher courses ensure operators stay updated on equipment changes and safety procedures.
- Enhancing Situational Awareness: Situational awareness is crucial for operators to identify hazards early. Training should emphasize vigilance, risk anticipation, and awareness of surroundings. Practices like 360-degree checks and work area scans help reduce environment-related near misses.
- Clear Communication Protocols: Clear communication is crucial on busy sites with multiple teams. Standardized methods like radios, hand signals, or spotters help operators and personnel stay aware, quickly sharing vital information to prevent misunderstandings and near misses.
- Implementing Safety Checklists and Job Hazard Analyses: Safety checklists and job hazard analyses (JHAs) help identify job-specific risks. Checklists ensure all safety measures are confirmed, while JHAs identify hazards and controls, making safety practices routine and preventing oversights that cause near misses.
- Encouraging a Culture of Safety and Near Miss Reporting: A safety-focused culture encourages workers to report near misses and hazards freely, providing valuable insights for preventing incidents. An open, non-punitive reporting environment turns close calls into opportunities for safety improvements.
- Adopting Telematics Technology: Telematics technology allows real-time monitoring of machinery, providing critical insights into equipment performance and potential issues. By analyzing data such as engine health, hydraulic pressure, and brake systems, telematics helps identify malfunctions before they escalate. This proactive approach enhances operational safety, prevents costly downtime, and significantly reduces the risk of near misses, ensuring a more reliable and efficient work environment for heavy equipment operations.
Conclusion: The Value of Learning from Near Miss incidents.
Near miss events offer valuable insights for improving safety in high-risk sectors like construction, mining, forestry, and agriculture. By identifying, documenting, and analyzing these incidents, organizations can proactively address potential hazards and prevent serious accidents. Utilizing near miss data fosters a safety-focused culture, where employees feel empowered to report risks, enabling proactive risk management.
Through consistent trend analysis, companies can identify patterns, understand root causes, and implement targeted solutions—whether through technology, improved communication, or training. This approach not only reduces accidents and downtime but also builds trust, morale, and team ownership of workplace safety. Over time, near miss reporting and analysis become foundational for ongoing safety improvements, reinforcing a resilient safety culture dedicated to continuous advancement.
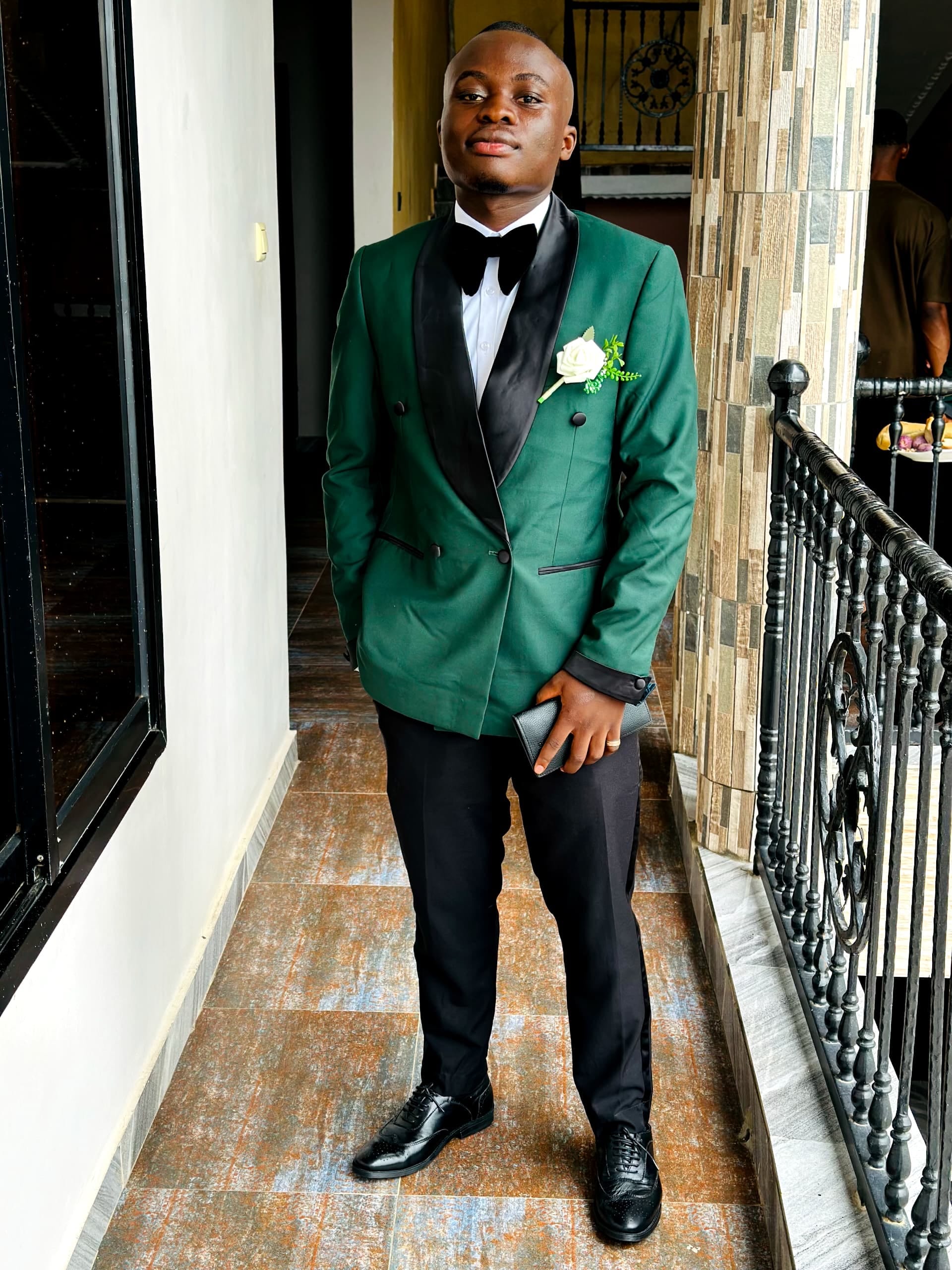
Ningo, founder of Big Machines Today, is a passionate writer and content creator specializing in heavy-duty machinery. Focused on delivering industry insights and trends, Ningo crafts engaging content for professionals. Open to free collaborations on blogs or social media articles, Ningo invites you to connect and explore the Big Machines Today Blog for valuable updates.
[…] appropriate speeds, and following established safety guidelines) is essential to minimize risks and near miss events hence preventing accidents and enhancing operator safety. These practices not only protect the […]
[…] likelihood of errors, and significantly improves safety on construction sites by greatly reducing near miss events, creating a more productive, reliable, and safer working environment for all […]
[…] protocols diligently are all critical measures to minimize risks. These practices not only prevent near-miss events and accidents but also foster a secure working environment for everyone on the job […]