Regular heavy equipment repairs, part replacements, and unexpected breakdowns can strain your budget and reduce overall profitability. However, with the right strategies in place, businesses can significantly cut these costs while improving the lifespan and efficiency of their equipment. Discover 10 effective strategies to minimize expenses on heavy equipment repairs and enhance your profitability. By implementing these strategies, companies can save money, reduce downtime, and maximize the value of their heavy-duty machinery investments.
Table of Contents
1. Implement a Preventative Maintenance Program.
A well-structured preventative maintenance program is essential for reducing repair costs and minimizing downtime in heavy-duty machinery. By scheduling regular checks and maintenance, you can avoid unexpected breakdowns and the costly repairs that follow. Key preventative measures include:
- Regular oil changes and fluid top-ups.
- Timely replacement of filters (air, oil, fuel, and hydraulic).
- Routine inspections of belts, hoses, and tires.
- Lubrication of moving parts.
- Cleaning equipment to prevent debris buildup
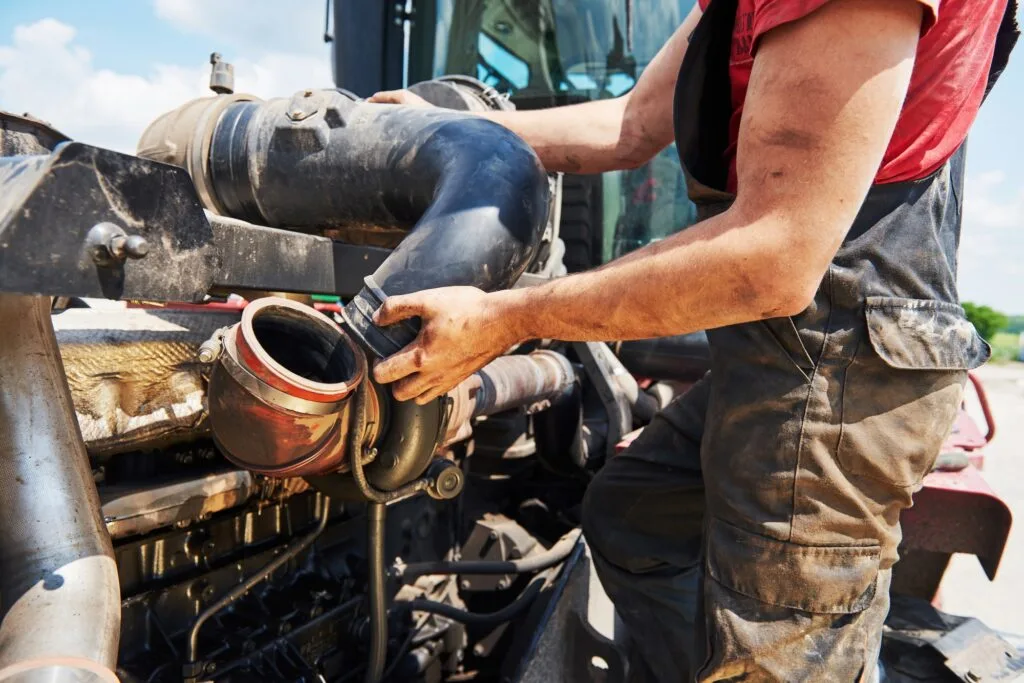
These proactive steps ensure that your equipment operates efficiently and lasts longer. For example, regularly changing filters keeps contaminants from damaging vital engine components, while proper lubrication reduces wear on moving parts.
The long-term savings are considerable. Preventative maintenance helps identify minor issues before they turn into expensive problems, saving up to five times the investment. Additionally, well-maintained machinery runs more efficiently, lowering fuel and energy consumption, leading to further savings.
Overall, adopting a preventative maintenance schedule not only reduces costs on repairs but also boosts productivity by minimizing unplanned downtime. This approach enhances the reliability and longevity of your equipment, making it a smart investment for any fleet owner.
2. Train Your Operators.
Investing in comprehensive operator training programs is a vital strategy for reducing costs on repairs. Skilled operators play a critical role in enhancing both productivity and the longevity of equipment, effectively minimizing the frequency of repairs and reducing wear and tear.
Properly trained operators can increase equipment productivity by up to 50% and reduce costs on repairs by around 25%. These trained individuals handle machinery more efficiently, using less fuel and causing fewer mechanical issues. Key benefits of operator training include:
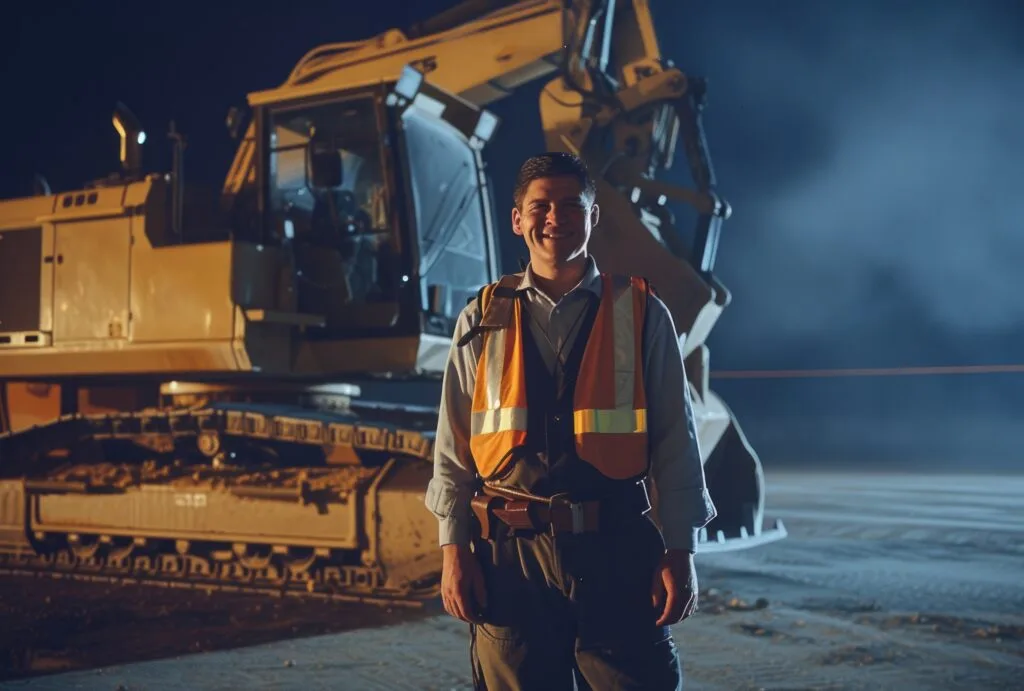
- Improved safety: Reduces the risk of accidents and damage.
- Prolonged equipment life: Ensures machinery is used correctly, preventing premature wear.
- Fuel savings: Skilled operators typically reduce fuel consumption by 10-12% daily.
- Better problem-solving: Operators can troubleshoot issues on-site, preventing minor problems from escalating.
- Enhanced communication: Promotes better coordination among team members.
On the other hand, improper use of equipment can lead to faster deterioration, such as overloading, incorrect control operations, poor storage, and neglected maintenance checks. By prioritizing operator training, businesses can substantially lower costs on repairs, extend equipment lifespan, and boost overall efficiency, making the investment in training both cost-effective and crucial for long-term success.
3. Utilize Telematics for Predictive Maintenance.
Telematics technology has transformed the way repairs is approached, enabling businesses to shift from reactive to predictive maintenance. By gathering real-time data from connected machinery, telematics systems can forecast potential issues before they cause significant problems, helping to reduce downtime and costs on repairs.
These systems monitor critical metrics such as engine performance, fluid levels, and component temperatures. Using advanced analytics and machine learning, telematics can identify patterns that indicate potential failures. For instance, if a machine’s engine temperature consistently rises above normal, the system can predict an overheating issue and alert operators to take preventive action. The key benefits of predictive maintenance through telematics include:
- Early Detection: Problems can be identified weeks in advance, allowing for timely repairs.
- Reduced Downtime: Addressing issues before they escalate helps minimize unexpected breakdowns.
- Optimized Maintenance: Maintenance can be scheduled based on actual equipment condition, not just on fixed intervals.
- Extended Equipment Life: Prompt attention to issues reduces wear and tear, extending the lifespan of machinery.
- Cost Savings: Predictive maintenance can cut maintenance costs by 5-10%.
By adopting telematics, businesses can enhance equipment efficiency, reduce heavy equipment repairs cost, and ensure that their machinery remains in peak condition, maximizing uptime and performance.
4. Establish a Proper Lubrication Schedule.
Proper lubrication is essential for the longevity and efficiency of heavy equipment. It forms a protective layer between moving parts, minimizing friction, wear, and excessive heat buildup. An effective lubrication schedule can extend the life of machinery, enhance performance, and reduce overall costs on repairs.
Failing to lubricate equipment correctly or using the wrong lubricants can lead to several issues, including:
- Increased wear and premature failure of components.
- Higher energy consumption and operating temperatures.
- Contamination and corrosion of parts.
- More frequent breakdowns and unplanned downtime.
- Higher repair and maintenance expenses
To develop an effective lubrication plan:
- Identify lubrication points on each machine.
- Choose the right type and amount of lubricant for each part.
- Set lubrication intervals based on usage and working conditions.
- Use a Computerized Maintenance Management System (CMMS) to schedule and track lubrication tasks.
- Train staff on proper lubrication techniques and safety protocols.
- Regularly update the lubrication schedule based on equipment performance
A well-executed lubrication plan ensures your equipment receives the correct lubricant at the right time, helping to prevent unnecessary repairs, reduce downtime, and improve overall efficiency.
5. Optimize Spare Parts Inventory.
An efficient spare parts inventory is essential for minimizing maintenance costs, overall costs on repairs and reducing equipment downtime. By ensuring that commonly used parts are readily available, businesses can avoid costly emergency repairs and prevent production delays.
Buying high-quality parts in bulk, when appropriate, can offer considerable savings. Bulk purchasing typically reduces the per-unit cost and lowers shipping expenses, while also guaranteeing a steady supply of essential components. This minimizes the risk of unexpected shortages that could disrupt operations. To effectively manage your spare parts inventory, consider these strategies:
- Implement a computerized maintenance management system (CMMS) to monitor inventory levels, track usage, and automate reordering.
- Use ABC analysis to prioritize parts based on consumption and XYZ analysis to assess demand variability, helping to determine which parts to stock in abundance and which to reorder as needed.
- Apply QR labels or unique identifiers to each part for better tracking and fewer errors.
- Regularly audit your inventory to phase out obsolete or slow-moving parts, improving storage efficiency and freeing up working capital.
- Establish clear reordering procedures with optimal reorder points to maintain lean inventory levels while ensuring critical components are always available.
By optimizing your spare parts inventory, you can significantly reduce maintenance costs, enhance operational efficiency, and keep your heavy equipment running smoothly with minimal downtime.
6. Invest in Regular Equipment Inspections.
Regular and comprehensive equipment inspections are vital to maintaining heavy machinery efficiently. These inspections help identify potential issues early, preventing them from developing into major problems that could lead to costly heavy equipment repairs and unplanned downtime. By establishing a consistent inspection program, you can:
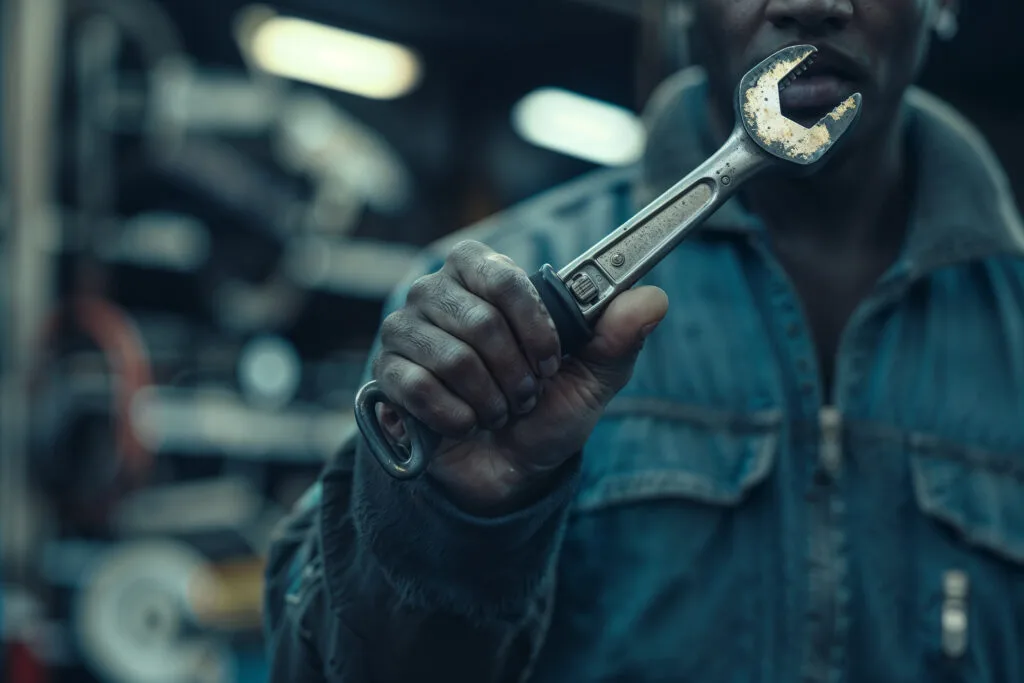
- Identify signs of wear and tear early, enabling prompt repairs.
- Minimize unexpected breakdowns and reduce downtime.
- Extend the life of your equipment.
- Ensure compliance with safety regulations
For example, catching a small hydraulic leak during an inspection can be a simple fix, such as replacing a seal. However, neglecting this issue could lead to severe damage requiring costly repairs. Certified inspectors bring expert knowledge and use advanced techniques (such as vibration analysis, oil testing, and thermal imaging) to thoroughly assess your machinery. This proactive maintenance strategy can reduce maintenance costs by up to 40% and downtime by as much as 50%, protecting both your equipment and business operations.
7. Use High-Quality Parts and Consumables.
Selecting high-quality parts and consumables is essential for maximizing the performance and lifespan of your heavy machinery. While cheaper alternatives may seem appealing at first, the long-term consequences can be costly. Subpar parts often lack the durability needed for heavy equipment, leading to increased wear, more frequent breakdowns, and ultimately higher maintenance expenses.
In contrast, premium parts are engineered to endure the rigorous demands of heavy machinery, ensuring better performance and a longer lifespan. Although the initial investment in high-quality parts may be higher, the long-term savings are substantial. Studies indicate that every dollar spent on quality preventative maintenance can save up to five dollars in unplanned repair costs.
To ensure you’re getting cost-effective yet reliable parts it’s important to:
- Consult the manufacturer’s recommendations for compatible components.
- Source parts from trusted dealers who specialize in your equipment type.
- Consider OEM (Original Equipment Manufacturer) parts for superior fit and reliability.
- Explore remanufactured parts from reputable suppliers as a more affordable alternative to new OEM parts.
- Always inspect parts before purchase to verify they meet required specifications.
By choosing quality over short-term savings, you’ll experience improved performance, less downtime, and a lower total cost of ownership for your equipment.
8. Extend Equipment Life with Proper Storage.
Environmental factors such as temperature fluctuations and moisture can greatly affect the performance and longevity of heavy machinery. Exposure to extreme conditions can lead to high costs on repairs and reduced efficiency.
- Temperature effects:
- Heat: High temperatures can cause metal components to expand, leading to warping or misalignment.
- Cold: Low temperatures can thicken hydraulic fluids, affecting system responsiveness and lifting capacity.
- Fluctuations: Repeated expansion and contraction can crack metals and damage internal parts.
- Moisture concerns:
- High humidity accelerates corrosion and rusting of metal components.
- Moisture can also cause electrical malfunctions, increasing the risk of short circuits.
To protect your equipment during downtime, follow these storage tips:
- Store machinery in an enclosed, insulated space such as a garage, barn, or warehouse.
- Keep the storage area clean, dry, and free from pests.
- Use protective mats for tracked equipment to prevent floor damage.
- Cover equipment with heavy-duty tarps to shield it from moisture.
- Clean both the exterior and interior thoroughly before storage and lubricate moving parts as per manufacturer instructions.
Benefits of proper storage:
- Protection from extreme weather conditions.
- Prevention of moisture buildup, mold, and rust.
- Shielding from dust, debris, and pests.
- Improved air quality, preserving sensitive materials and electronics.
By following these storage practices, you can extend your equipment’s lifespan, reduce maintenance costs, and ensure it’s ready for optimal performance when needed again.
9. Leverage Extended Warranties and Service Contracts.
Extended warranties and service contracts offer significant long-term cost savings for heavy equipment owners. While standard warranties typically cover equipment for about two years, extended options can provide protection for up to five years or 700,000 kilometers, ensuring greater cost predictability and peace of mind.
The main advantages of extended warranties over standard coverage include:
- Longer Duration: Extended warranties last beyond the typical two-year coverage period.
- Broader Scope: They often cover a wider range of components and systems, including critical parts like engines, transmissions, and hydraulics.
- Cost Efficiency: While there’s an upfront cost, extended warranties can protect against expensive repairs and minimize unplanned expenses.
These warranties can reduce downtime by ensuring expedited repairs and offering access to certified technicians and genuine OEM parts. For instance, a powertrain warranty might cover essential components like the engine, generator, and motor, which could save thousands in repair costs. Some extended warranty programs even include transport coverage to and from maintenance shops, further reducing unexpected costs.
By investing in these contracts, equipment owners can lower their total cost of ownership, enhance uptime, and maximize the equipment’s residual value. Though there is an initial investment, the return is substantial—studies show that for every dollar spent on preventative maintenance (often included in service contracts), up to five dollars can be saved in unforeseen expenses. This strategy not only protects against costly breakdowns but also ensures optimal equipment performance, supporting better business outcomes.
10. Invest on the Right Grade of Fuel.
Optimizing fuel quality is essential for minimizing maintenance costs and enhancing the performance of heavy-duty machinery. High-quality fuel ensures smoother engine operation, improves fuel efficiency, and reduces wear on critical components, leading to long-term savings. Using premium fuel with the correct cetane rating for your equipment provides several benefits:
- Improved engine performance and fuel efficiency.
- Reduced emissions and cleaner combustion.
- Extended equipment lifespan.
- Lower maintenance and repair costs.
In contrast, poor-quality fuel can cause significant issues, such as injector fouling, combustion instability, and excessive engine deposits. These problems increase wear and tear, potentially leading to engine failure and expensive repairs.
To ensure optimal fuel quality:
- Source fuel from reputable suppliers who follow industry standards.
- Choose fuel with additives like detergents, stabilizers, and lubricity agents.
- Use fuel with the proper cetane rating for your equipment, typically between 45 to 55 for modern diesel engines.
- Regularly test fuel for contamination and quality.
- Consider fuel additives to improve stability and performance.
Prioritizing fuel quality not only cuts maintenance costs but also enhances operational efficiency and prolongs the lifespan of your equipment. This simple yet effective measure contributes to both short-term savings and long-term reliability.
Conclusion.
In summary, the 10 strategies outlined in this article (ranging from implementing a preventative maintenance program to optimizing fuel quality) are all crucial for reducing heavy-duty machinery costs on repairs. By following these practical tips, you can enhance equipment performance, reduce downtime, and ultimately save on repairs.
We encourage you to start incorporating these strategies into your daily operations for long-term savings and greater equipment reliability. If you found this article useful, please share it with others in the industry. We’d love to hear your thoughts—drop a comment with any additional tips you believe would be helpful, or share your experiences with these strategies. Let’s keep the conversation going to help everyone in the heavy equipment community succeed.

Ningo, founder of Big Machines Today, is a passionate writer and content creator specializing in heavy-duty machinery. Focused on delivering industry insights and trends, Ningo crafts engaging content for professionals. Open to free collaborations on blogs or social media articles, Ningo invites you to connect and explore the Big Machines Today Blog for valuable updates.
Excellent advice! These strategies provide a solid plan for reducing repair costs and improving overall equipment maintenance.
Great insights on reducing heavy equipment repair costs! Preventive maintenance and proper operator training are definitely game-changers for long-term savings.